How Digital Twins Transform Construction Monitoring and Operations
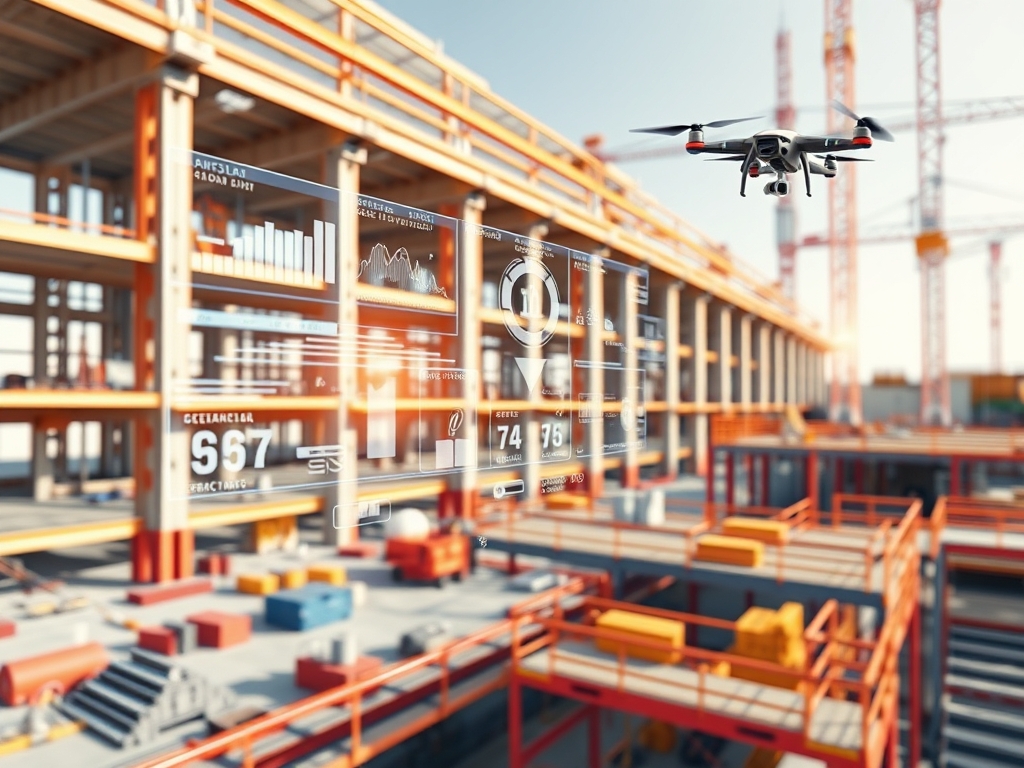
Construction is an industry of paradoxes. On one hand, it’s one of humanity’s oldest crafts, reliant on age-old practices and physical labor. On the other, it’s a fertile ground for innovation, where digital tools promise to revolutionize workflows and outcomes. Among these tools, digital twins stand out, not as a fleeting trend, but as the next fundamental shift in how we monitor and manage construction projects.
But the conversation around digital twins often focuses on the abstract—”bridging physical and digital worlds”—without cutting into the marrow of how they transform day-to-day construction realities. Let’s get specific.
Digital Twins: The Living, Breathing Heart of Construction Projects
Think of a digital twin not as a mere 3D model, but as a living entity. It mirrors the physical project in real-time, ingesting streams of data from sensors, drones, and IoT devices. But it doesn’t just reflect reality; it analyzes, predicts, and optimizes it. This shift from static plans to dynamic, evolving systems is akin to giving a construction site its own nervous system—one capable of seeing, sensing, and adapting.
Moving Beyond Schedules and Spreadsheets
In traditional construction workflows, schedules and spreadsheets are the command center. They’re also where critical information goes to stagnate. A delay on-site often takes hours—or even days—to ripple through to decision-makers. With digital twins, that delay evaporates.
- Real-Time Feedback Loops: Digital twins integrate with IoT sensors and drones to provide instant updates on progress, material deliveries, or bottlenecks. If a concrete pour is delayed, the twin recalibrates the project timeline instantly, highlighting downstream impacts.
- Proactive Problem-Solving: Instead of reacting to issues, teams can simulate different scenarios—what happens if crane availability changes, or weather conditions worsen? The twin provides actionable answers.
Example: A large infrastructure project in Europe leveraged a digital twin to track earth-moving equipment in real-time. By syncing geospatial data with operational goals, they cut idle times by 25% and saved millions.
Bridging the Communication Divide
Construction projects are plagued by siloed communication—designers speak in drawings, contractors in schedules, and project managers in dollars. A digital twin serves as a universal translator:
- For Designers: Real-time visualization of how designs translate to physical realities. No more “was this beam installed as planned?”
- For Contractors: An intuitive interface showing where progress aligns with (or diverges from) the plan.
- For Clients: A dashboard that reduces technical complexities into clear, understandable insights.
Operational Awareness at an Unprecedented Scale
On a construction site, what you don’t know can cost you. Digital twins make ignorance almost impossible by providing 360-degree awareness:
- Material Tracking: Know exactly where every brick, beam, and bolt is—both physically and in the timeline.
- Equipment Utilization: Track machinery to identify underuse or inefficiencies. Optimize fleets instead of overspending.
- Safety Insights: Monitor worker movements and environmental conditions to proactively prevent hazards.
A New Era of Predictive Construction Management
What sets digital twins apart isn’t just their ability to monitor the present—it’s their ability to anticipate the future. By layering predictive analytics onto real-time data, digital twins become crystal balls for construction managers.
- Risk Mitigation: Identify weak links in supply chains or potential delays before they occur.
- Budget Control: Simulate cost overruns in response to unexpected events and reallocate resources accordingly.
- Energy Efficiency: For green construction projects, twins analyze how materials and processes impact energy consumption, allowing for course corrections in real-time.
Opinion: Digital twins aren’t just enhancing efficiency; they are challenging the construction industry’s tolerance for waste and guesswork. In an era of razor-thin margins and increasing accountability, their adoption is not optional—it’s inevitable.
The Challenges Nobody Talks About
For all their promise, digital twins aren’t a magic wand. They demand substantial cultural and technical shifts, which the industry is not universally ready for.
- Data Overload: A twin is only as good as the data it receives. Inconsistent or incomplete data inputs can lead to flawed insights.
- Skill Gaps: Construction managers trained on analog methods may struggle to adapt to digital workflows. Bridging this gap requires significant investment in training and change management.
- Integration Pain Points: Not all tools and platforms play nicely together. Creating seamless ecosystems for digital twins to thrive remains a challenge.
The Transformative Potential for Operations
Post-construction, the value of a digital twin doesn’t end—it evolves. Once the building is operational, the twin transitions into a tool for facility management, integrating maintenance schedules, occupancy data, and energy optimization into one cohesive system. This continuity is the holy grail of the construction-to-operations lifecycle.
Example: A major airport uses a digital twin to monitor passenger flows, HVAC efficiency, and maintenance schedules. By integrating these data points, they’ve improved energy efficiency by 15% and reduced maintenance disruptions by 20%.
Final Thoughts: The New Blueprint for Construction
Digital twins are not an enhancement—they are a reinvention of how construction projects are planned, executed, and managed. They dissolve barriers between the physical and digital, enabling teams to operate with clarity, foresight, and precision.
The question is no longer whether the construction industry will adopt digital twins. The real question is how quickly firms can embrace the change and whether they’ll wield this technology as a competitive advantage or lag behind in an era that demands nothing less than transformation.