Optimizing Facility Management with Interactive 3D Models
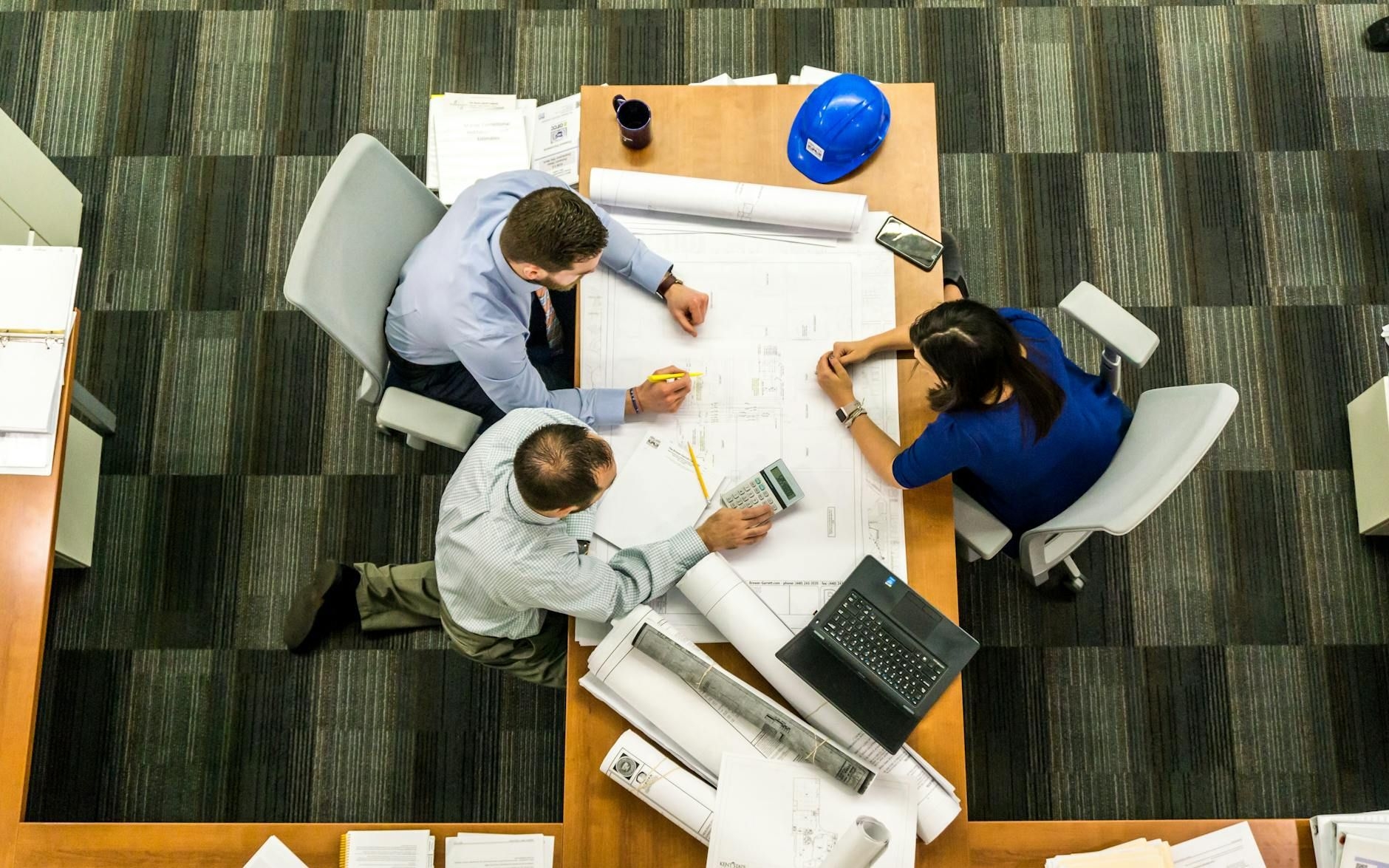
In the rapidly evolving field of facility management, the integration of interactive 3D models is revolutionizing how buildings are maintained and operated. This article examines how facility managers can harness the power of these digital tools to enhance maintenance planning and boost operational efficiency.
The Evolution of Facility Management
Traditionally, facility management relied heavily on 2D drawings, spreadsheets, and manual inspections. The advent of Building Information Modeling (BIM) and interactive 3D models has ushered in a new era of data-driven facility management. These digital twins of physical structures offer unprecedented insights into building systems and components.
Benefits of Interactive 3D Models in Facility Management
- Comprehensive Visualization: Interactive 3D models provide a holistic view of the facility, allowing managers to navigate through the entire building virtually.
- Real-time Data Integration: These models can be linked to IoT sensors, providing real-time data on equipment performance, energy consumption, and environmental conditions.
- Predictive Maintenance: By analyzing historical data and current performance metrics, facility managers can predict when equipment is likely to fail and schedule maintenance proactively.
- Streamlined Operations: 3D models centralize information, reducing the time spent searching for building data and improving response times to maintenance issues.
- Enhanced Collaboration: Interactive models facilitate better communication between facility managers, maintenance teams, and external contractors.
Implementing Interactive 3D Models for Maintenance Planning
Interactive 3D models serve as a comprehensive database for all building assets. Facility managers can:
- Tag equipment with detailed specifications, maintenance history, and performance data.
- Set up automated alerts for scheduled maintenance based on usage or time intervals.
- Quickly locate assets within the facility using the 3D interface.
Leveraging the data integration capabilities of 3D models, facility managers can:
- Create dynamic maintenance schedules based on real-time equipment performance.
- Prioritize maintenance tasks based on criticality and potential impact on operations.
- Optimize resource allocation by grouping maintenance tasks by location or type.
Interactive models streamline the work order process by:
- Allowing technicians to access detailed equipment information and repair histories on-site.
- Enabling the attachment of photos, videos, and notes directly to specific components in the 3D model.
- Facilitating the creation of step-by-step repair guides linked to equipment models.
Facility managers can use interactive 3D models to:
- Visualize and optimize space utilization.
- Plan renovations or reconfigurations with minimal disruption to ongoing operations.
- Conduct virtual walkthroughs for stakeholders during planning phases.
Enhancing Operational Efficiency
Interactive 3D models, when integrated with building management systems, can:
- Provide visual representations of energy consumption patterns throughout the facility.
- Simulate the impact of energy-saving measures before implementation.
- Identify areas of high energy consumption for targeted efficiency improvements.
3D models enhance safety and emergency preparedness by:
- Offering clear visualizations of evacuation routes and safety equipment locations.
- Simulating various emergency scenarios for better response planning.
- Providing first responders with detailed building layouts and critical system information.
For multi-tenant facilities, interactive models can:
- Simplify the process of tracking and managing tenant spaces.
- Facilitate more efficient move-in and move-out processes.
- Improve communication with tenants regarding maintenance activities or building updates.
Challenges and Considerations
While the benefits of interactive 3D models are significant, facility managers should be aware of potential challenges:
- Initial Implementation Costs: The upfront investment in technology and training can be substantial.
- Data Management: Ensuring data accuracy and keeping the model updated requires ongoing effort.
- Technology Integration: Seamlessly integrating 3D models with existing facility management systems may present technical challenges.
- User Adoption: Staff may require training and time to become proficient in using the new technology.
Future Trends
As technology continues to advance, we can expect to see:
- Increased integration of artificial intelligence for more sophisticated predictive maintenance.
- Augmented reality applications that overlay 3D model data onto the physical environment.
- Greater emphasis on sustainability metrics and carbon footprint management within 3D models.
Conclusion
Interactive 3D models represent a paradigm shift in facility management, offering unprecedented capabilities for maintenance planning and operational efficiency. By providing a centralized, data-rich visualization of the entire facility, these models empower facility managers to make informed decisions, optimize resources, and enhance overall building performance.
As the technology matures and becomes more accessible, adoption of interactive 3D models in facility management is likely to become standard practice. Forward-thinking facility managers who embrace these tools now will be well-positioned to lead the industry in operational excellence and sustainability.
The future of facility management lies in the intelligent use of data and visualization. Interactive 3D models are not just a technological advancement; they are a gateway to smarter, more efficient, and more responsive building management.